Working together for a sustainable textile business: Looking back at World Textile Forum 2019
The 2019 World Textile Forum closes its doors after two successful and exciting days.
On September 9 and 10 renowned speakers and experts from the textile business gathered in Zurich to discuss opportunities in the changing textile world. Exciting talks and keynotes illustrated new possibilities for a more sustainable and digital textile industry. While one part of the versatile program focussed on “Sustainable Sourcing” with speakers such as Robert van de Kerkhof (Lenzing AG), Heinz Zeller (Hugo Boss), Daniel Gemperle (Calida) and Anna Maria Rugarli (VF), the topic of “Digital Production” became the centre of attention later thanks to experts like Torbjörn Netland (ETH), Maximilian Kürig (Karl Mayer), Maria Neidhold (Spoonflower) and Holger Max-Lang (Lectra). They offered new perspectives on the sustainable future of the textile industry, presenting innovative sustainable production and business models. The subsequent panels furthered the knowledge exchange between both attendees and speakers and led to lively discussions.
Swiss Textile Federation, Swiss Textile & Fashion Institute STF and Gherzi Textil Organisation would like to thank all attendees and look forward to the next World Textile Forum!
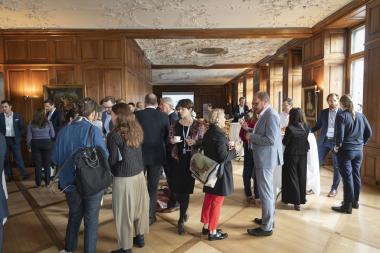
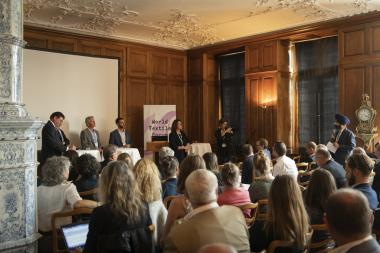
World Textile Forum Schweizerischen Textilfachschule STF Gherzi Textil Organisation Nachhaltigkeit Swiss Textiles
Schweizerische Textilfachschule STF